Friday, June 09, 2017
Wednesday, July 06, 2016
by Dave Smith
Drying roughed turned bowls has always been a challenge for wood turners. You need to balance the desire to finish a piece as soon as possible with the inherent tendency of wood to warp and split when dried too quickly. Wood turners have employed various methods to maximize the drying speed while minimizing the degradation of the wooden shape being created. Over time each method has collected its own supporters and detractors with respect to the relative effectiveness of the process.
Criteria for a good drying process include ease of use, cost, and consistency of results. A process that is difficult to use, even though it produces good results, will garner few adherents. Likewise, an expensive protocol may appeal to a commercial turner who can expect to recoup the investment but it may be cost prohibitive for the average wood turner. Consistent results without labor intensive monitoring or manipulations are a major benefit of any method.
The most common method of drying wood bowls is placing them in a paper grocery bag. The theory is that the permeable paper produces a micro climate around the bowl. The bowl dries slowly with a small differential moisture gradient across the bowl sides. This method works well but it is slow.
Boiling can improve the stability of the wood by rupturing the cells, allowing moisture to more readily migrate to the surface and evaporate. Boiling is time and labor intensive, consuming requiring considerable space for a large pot and heat source. Since most people don't want to boil bowls in the kitchen, it is necessary to set up some way to boil outdoors which can be a big drawback in cooler climates during the winter months. Boiling can also be dangerous. A good friend of mine was severely burned when a plate blank wedged in a boiling pot of water, sealed the pot and led to a steam explosion.
Soap soaking has gained popularity in recent years. A bowl soaked in a soap solution is supposed to be easier to turn because of the lubricating action of the soap. Bowls are said to dry faster and crack less after soaking but some people report that there is still a fair amount of distortion of the finished piece.
It was my experience with soap soaking that led me to the alcohol soaking procedure I use today. When I researched soap soaking and read the discussions on wood working forums, the consensus was that it was the surfactant in soap that allowed the wood to dry faster.
Researching the MSDS (material safety data sheets) for several commonly used soaps revealed that the surfactants were listed as being alcohols. I reasoned that using alcohol for a soaking solution might be a simpler method. The most readily available alcohol is denatured alcohol found in the paint section of any hardware store. A gallon of denatured alcohol costs from 10 to 12 dollars.
A search on the internet noted several instances of alcohol soaking of archeological artifacts to displace water in a complicated protocol for stabilizing and preserving historical wood pieces. Alcohol soaking is used as the first step in of a process to replace water in the wood with a stable inert binder that will maintain the shape of the artifact and prevent further degradation. The fact that alcohol is used to displace water in archeological artifacts suggests that it might also work to displace water in green wood thus speeding up the drying process.
My testing involved a large variety of wood species. In each case, the results have been consistently good. Types of wood included some traditionally hard to dry woods such as apple, plum, cherry and mulberry.
The test consisted of turning two similarly sized bows from the same type wood. One bowl from each sample was soaked in alcohol then both were dried in the same manner. Several methods of drying were used from the most conservative, a paper bag, to the most radical of placing the bowls uncovered on a wire rack in my heated, dehumidified shop. I recorded the weight, date and time when the bowl was set aside for drying and then recorded the weight daily when possible. After the bowl stopped losing weight it was considered dry or at equilibrium with the surroundings. The data showed that small thin (1/2 inch thick walls) bowls would reach equilibrium in 4 to 5 days. Using this data, I developed a process that was quick and consistently yielded usable bowls.
Criteria for a good drying process include ease of use, cost, and consistency of results. A process that is difficult to use, even though it produces good results, will garner few adherents. Likewise, an expensive protocol may appeal to a commercial turner who can expect to recoup the investment but it may be cost prohibitive for the average wood turner. Consistent results without labor intensive monitoring or manipulations are a major benefit of any method.
The most common method of drying wood bowls is placing them in a paper grocery bag. The theory is that the permeable paper produces a micro climate around the bowl. The bowl dries slowly with a small differential moisture gradient across the bowl sides. This method works well but it is slow.
Boiling can improve the stability of the wood by rupturing the cells, allowing moisture to more readily migrate to the surface and evaporate. Boiling is time and labor intensive, consuming requiring considerable space for a large pot and heat source. Since most people don't want to boil bowls in the kitchen, it is necessary to set up some way to boil outdoors which can be a big drawback in cooler climates during the winter months. Boiling can also be dangerous. A good friend of mine was severely burned when a plate blank wedged in a boiling pot of water, sealed the pot and led to a steam explosion.
Soap soaking has gained popularity in recent years. A bowl soaked in a soap solution is supposed to be easier to turn because of the lubricating action of the soap. Bowls are said to dry faster and crack less after soaking but some people report that there is still a fair amount of distortion of the finished piece.
It was my experience with soap soaking that led me to the alcohol soaking procedure I use today. When I researched soap soaking and read the discussions on wood working forums, the consensus was that it was the surfactant in soap that allowed the wood to dry faster.
Researching the MSDS (material safety data sheets) for several commonly used soaps revealed that the surfactants were listed as being alcohols. I reasoned that using alcohol for a soaking solution might be a simpler method. The most readily available alcohol is denatured alcohol found in the paint section of any hardware store. A gallon of denatured alcohol costs from 10 to 12 dollars.
A search on the internet noted several instances of alcohol soaking of archeological artifacts to displace water in a complicated protocol for stabilizing and preserving historical wood pieces. Alcohol soaking is used as the first step in of a process to replace water in the wood with a stable inert binder that will maintain the shape of the artifact and prevent further degradation. The fact that alcohol is used to displace water in archeological artifacts suggests that it might also work to displace water in green wood thus speeding up the drying process.
My testing involved a large variety of wood species. In each case, the results have been consistently good. Types of wood included some traditionally hard to dry woods such as apple, plum, cherry and mulberry.
The test consisted of turning two similarly sized bows from the same type wood. One bowl from each sample was soaked in alcohol then both were dried in the same manner. Several methods of drying were used from the most conservative, a paper bag, to the most radical of placing the bowls uncovered on a wire rack in my heated, dehumidified shop. I recorded the weight, date and time when the bowl was set aside for drying and then recorded the weight daily when possible. After the bowl stopped losing weight it was considered dry or at equilibrium with the surroundings. The data showed that small thin (1/2 inch thick walls) bowls would reach equilibrium in 4 to 5 days. Using this data, I developed a process that was quick and consistently yielded usable bowls.
The Process:
Bowls are roughed out to 1/2 inch wall thickness for pieces less than 8" in diameter. Over 8" in diameter, I leave a wall thickness of 5/8 to 3/4 inches. Since my lathe is limited to 12 inches, I have not tested bowls larger than that for optimum wall thickness. I often turn utility pieces with a finished wall thickness of a quarter to half an inch. In these cases the roughed out wall thickness needs to be thick enough to allow for distortion. No drying method will completely prevent movement of the wood when it dries, so plan your roughed out blank accordingly.
Once the bowl is roughed out it is submerged in denatured alcohol for at least 2 hours. Larger, thicker bowls need to soak longer to ensure good penetration of the alcohol. Longer soaking time does not appear to damage the wood.
Now wrap the outside of the bowl in heavy paper such as a grocery bag. Secure the paper with a couple of wraps of masking tape around the rim. Fold the paper over the rim, trim off the excess, and place the bowl upside down on a rack to dry. If the bowl set on the foot it may not rest evenly due to the paper and the air may not circulate as well. The inside of the bowl needs to be exposed to air.
The reason for wrapping the outside only is the theory that it will create a compressive stress on the bowl by drying the inside quicker than the outside. As the inside dries it shrinks which pulls on the outside causing it to compress. This compressive force minimizes cracking during the drying process. Thinner walls yields less distortion and fewer cracks by decreasing the maximum stress developed between the inside and the outside.
The alcohol I use for soaking bowls is denatured ethanol alcohol, straight from the can. I do not recommend methanol due to health and safety concerns. Although I did sucessfully test some bowls in isopropyl alcohol I did not like the smell. Isopropyl is not readily available in concentrations greater than 70% while denatured ethanol normally is 95%. Alcohol is added to a container as needed to cover pieces. During soaking, some alcohol will be absorbed, so a small amount will be lost when each bowl is removed and must be replaced with fresh alcohol. Because of this I have not worried about the dilution of the solution over time. The results have been consistent for bowls soaked in fresh alcohol and those soaked in solution used many times.
One concern was the possibility that alcohol used to soak dark wood would become a dye and discolor lighter colored wood subsequently soaked in the solution. There has been no indication of this happening.
The solution does collect wood dust and other debris over a period of time, so I strain the solution when transferring between containers. A kitchen strainer place across a container with a paper towel filter is sufficient to remover the big hunks.
Containers used for storing soaking alcohol should be non metallic. Alcohol is about 95% alcohol and 5% water when purchased. As bowls are soaked in it, the moisture content of the solution will increase, which, along with other impurities leached from the wood will attack metal containers.
I use plastic ice cream containers for soaking bowls and storing used alcohol. A one gallon container will accommodate a bowl 8" in diameter by 5" tall. A two gallon ice cream container will hold a turning 8 1/4" in diameter and nearly 10 inches tall.
For larger bowls, a 13qt stainless steel bowl will accommodate 13" diameter bowls that are less than 6" from the rim to the bottom of the foot.
To cover a large bowl, place a sheet of heavy plastic film over the steel bowl and secure it by wrapping the rim with clear packing tape. If you stretch the tape, the cover can be removed and replaced as needed while providing a reasonably good seal.
Still larger bowls can be placed in a heavy plastic bag and then nested into a pile of shaving to conform to the bottom of the bowl and limit the amount of alcohol needed to cover the bottom. The inside of the bowl can also be filled to reduce the volume of alcohol needed to completely cover the bowl. With a little bit of ingenuity the amount of alcohol required to process large bowls can be held to a reasonable quantity.
Other Trials:
In order to verify the results I had obtained with alcohol soaking, I asked several other tuners to try it. I wanted to get a cross section of turners with different experiences and specialties. Some of those who provided data included Bill Grumbine, Dominic Greco, Mark Kauder, and Jennifer Shirley.
Mark Kauder has used the method for 3 bowls, two from box elder and one from sycamore. He bought a slab of freshly cut Ambrosia Sycamore, 4" thick and not sealed. He cut three 16" diameter blanks from it, roughed them out, then used the alcohol soaking method on one of them while completely covering the other two with Anchorseal. When he later pulled them out, the Alcohol Soaked on seemed dry, and had warped only about 1/2" across the grain. When he turned it, it was dry, and has not moved since. The two Anchorsealed ones had both warped/shrunk 1" across the grain and had "Potato chipped" or cupped about 1/2". After chucking them up and getting them round again, they still continued to move. Mark reports he will use the alcohol soaking method when he turns solid Wood.
Dominic Greco has completed more than a dozen pieces using the alcohol soaking process. He has used the process on many types of wood including; Box Elder, Norway Maple, Osage Orange, Cherry, Chinese Elm, and Apple. When asked what the worst problem was Dominic responded, "The piece of Osage Orange cracked during drying, but I believe this was a crack that was present in the blank, and not a direct result of drying". Dominic uses a moisture meter to determine when a bowl has completed drying. After 2 weeks he reports that his pieces are at a moisture content of 6%. None of his finished pieces have distorted as of the writing of this article, and Dominic reported that it is now the only method he uses for drying bowls.
Bill Grumbine used the alcohol soaking method in late 2003 to fill Christmas orders he received during a Thanksgiving artist show. Bill has been an enthusiastic supporter of the method.
Jennifer Shirley soaked one walnut bowl before reading the fine print as, she calls it, and left it in the alcohol for four days. When she removed it, she simply left it on a shelf exposed to air. Four months later the bowl exhibited no problems other than the normal out of round when she finished turning it.
Conclusions:
Although I collected data in a consistent manor and attempted to control variables, this is not a strict scientific study. The study did not verify my theory of why the process works. The study does show that soaking green roughed out bowls in alcohol does reduce the time necessary to bring them to equilibrium with their surroundings. Wrapping the outside of a bowl reduces distortion and checking. Testing by other wood tuners has verified that the protocol works consistently. The process is simple and relatively fast. The expense of denatured alcohol is minimal compared to the savings in reduced bowl losses, but the biggest saving is time. Using the alcohol soak method reduces the drying time for roughed out bowls from months to weeks.
. . . Dave Smith

© 2003 by Dave Smith . All rights reserved.
No parts of this article may be reproduced in any form or by any means
without the written permission of the author.
Friday, May 25, 2007
Presentation at SWAT
I will be a demonstrator at SouthWest Association of Turners(SWAT) symposium October 5-7, 2007 in Wichita Falls, Texas. The presentation will be on drying turned pieces using the alcohol drying protocol I developed.
At the present time there are two sessions scheduled.
Key points
• Development of the alcohol drying protocol
• Methanol and ethanol health and safety
• Understanding Material Safety Data Sheets (MSDS)
• Alcohol drying protocol
• Determining alcohol concentration in a solution
• Removing water from used soaking solution
Attendees will learn
• Alcohol soaking protocol theory
• Difference between methanol and ethanol health threat
• How to process a roughed turned bowl
• Determining when a roughed turned bowl is dry
• What a MSDS is for and how to decipher it
• How to determine alcohol concentration
See you at SWAT.
At the present time there are two sessions scheduled.
Key points
• Development of the alcohol drying protocol
• Methanol and ethanol health and safety
• Understanding Material Safety Data Sheets (MSDS)
• Alcohol drying protocol
• Determining alcohol concentration in a solution
• Removing water from used soaking solution
Attendees will learn
• Alcohol soaking protocol theory
• Difference between methanol and ethanol health threat
• How to process a roughed turned bowl
• Determining when a roughed turned bowl is dry
• What a MSDS is for and how to decipher it
• How to determine alcohol concentration
See you at SWAT.
Wednesday, November 29, 2006
Vine Maple Goblet
On Wood Central’s Turning Forum Steven Lewis asked about turning goblets from green wood. I decided to give it a try using the alcohol drying method. The only green wood readily available to me is vine maple.
The limb was about 2 ½" in diameter. As you can see the limb was not straight so I expected the stem would warp when drying.
The roughed out goblet is about 2" in diameter and 6" long. and the stem is ½" in diameter.
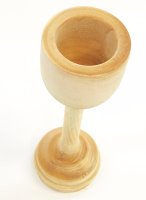
The piece soaked over night for my convenience. An hour or two in the alcohol would have probably been sufficient. After removing from the soaking container the goblet is wrapped in paper leaving the bowl uncovered.
Weight in Grams.
11/20 - 1000 - 143
11/21 - 0830 - 117
11/22 - 0700 - 110
11/24 - 2130 - 106
11/25 - 1230 - 106
11/25 - 2100 - 105
11/26 - 1300 - 106
11/27 - 1100 - 105
At 10:00AM November 20th the goblet weighed 143g. Four and a half days later it weighed 106g. By the 27h it hadn’t lost anymore weight so I finished turned the goblet.
With the tool rest set at the center line I adjusted the goblet to have the stem centered.
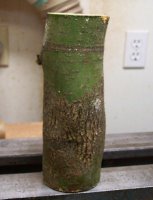
The roughed out goblet is about 2" in diameter and 6" long. and the stem is ½" in diameter.
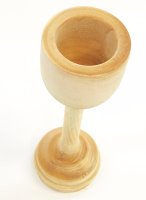
The piece soaked over night for my convenience. An hour or two in the alcohol would have probably been sufficient. After removing from the soaking container the goblet is wrapped in paper leaving the bowl uncovered.
Weight in Grams.
11/20 - 1000 - 143
11/21 - 0830 - 117
11/22 - 0700 - 110
11/24 - 2130 - 106
11/25 - 1230 - 106
11/25 - 2100 - 105
11/26 - 1300 - 106
11/27 - 1100 - 105
At 10:00AM November 20th the goblet weighed 143g. Four and a half days later it weighed 106g. By the 27h it hadn’t lost anymore weight so I finished turned the goblet.
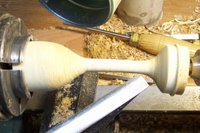
Yew box.
This yew wood came from a tree that had died during the previous summer. Recently cut down the wood was wet but not as wet as a live tree freshly cut. Other turners got to the tree first so I am left with smaller limbs to work with. A box was hollowed from a limb section.
The top portion roughed out to 1/4" wall thickness. The inside is rounded to a center thickness of approximately 3/8. The bottom portion roughed out to 5/16" thickness. The inside rounded to a center thickness of approximately ½".
The pieces soaked in alcohol overnight for my convenience. An hour or two in the alcohol would have probably been sufficient.
After removing from the container the two pieces were butted end to end with the box interior exposed on each end.
This procedure for wrapping boxes was instigated by Ron Sardo, or was it Phil Duffy, shortly after I published the alcohol drying procedure in November of 2004.
Wraped and on the drying rack.
11/20 - 1000 - 126
11/21 - 0830 - 111
11/22 - 0700 - 109
11/24 - 2130 - 108
11/25 - 1230 - 108
11/25 - 2100 - 108
11/26 - 1300 - 108
At 10:00AM November 20th the box weighed 126g. Four and a half days later it weighed 108g. By the 26h it hadn’t lost anymore weight so I finished turned the box.
No degradation and very little warping.
In retrospect I should have turned the sap wood away when rough turning to reveal the rich colored heartwood. I will do that with the next box I turn from a yew limb.
The top portion roughed out to 1/4" wall thickness. The inside is rounded to a center thickness of approximately 3/8. The bottom portion roughed out to 5/16" thickness. The inside rounded to a center thickness of approximately ½".
The pieces soaked in alcohol overnight for my convenience. An hour or two in the alcohol would have probably been sufficient.
After removing from the container the two pieces were butted end to end with the box interior exposed on each end.
This procedure for wrapping boxes was instigated by Ron Sardo, or was it Phil Duffy, shortly after I published the alcohol drying procedure in November of 2004.
Wraped and on the drying rack.
11/20 - 1000 - 126
11/21 - 0830 - 111
11/22 - 0700 - 109
11/24 - 2130 - 108
11/25 - 1230 - 108
11/25 - 2100 - 108
11/26 - 1300 - 108
At 10:00AM November 20th the box weighed 126g. Four and a half days later it weighed 108g. By the 26h it hadn’t lost anymore weight so I finished turned the box.
No degradation and very little warping.
In retrospect I should have turned the sap wood away when rough turning to reveal the rich colored heartwood. I will do that with the next box I turn from a yew limb.
Thursday, November 23, 2006
Determining Alcohol Percentage
Calculating alcohol concentration by weight.
The phenomenon of miscibility is key to drying wood by alcohol soaking. Miscible liquids will reach a uniform concentration when combined in a container. An example is a bottle of wine which maintains a uniform consistency of alcohol and water no matter how long it sets undisturbed.
When a piece of wood is placed in an alcohol solution the phenomenon of miscibility will cause the water in the wood and the alcohol in the solution to migrate until they reach equilibrium. The final alcohol concentration in the wood will always be less than the starting alcohol concentration of the soaking solution.
Replacing water in wood with alcohol is the key mechanism for drying wood faster. Alcohol readily moves through cell walls and has a lower vapor pressure than water. As the concentration of alcohol in the wood goes down the drying time increases. Therefore, it is useful to know the alcohol concentration of the soaking solution.
A hydrometer is one way to measure alcohol concentration. To be more accurate the temperature of the solution needs to be measured to correct for density changes due to temperature. The easiest way to measure temperature is to use a hydrometer with an integrated thermometer. Hydrometers are expensive and breakable. Since a scale is needed to track the drying of wood pieces a method of determining alcohol concentration by weight would utilize existing equipment and minimize cost.
Knowing that alcohol and water have different densities I concluded that the alcohol concentration of a solution could be calculated by a ratio of weights. I contacted Professor Shawn Bearden in Pocatello, ID and ask him if he could help me devise a procedure. Shawn developed the graph and table used in this procedure.
The procedure requires the following:
A scale capable of measuring a minimum of 1 gram(g) increments.
A see through container with a narrow neck to increase the accuracy of the sample size to be weighed.
A copy of the Alcohol Percentage Graph and Table
609g /527g = 1.155597
The resulting quotient is the ratio and will be a number greater than 1.
Rounded to 4 dismal places, ratio = 1.1556
Converting the quotient to percentage of alcohol concentration.
Using the graph find the ratio on the horizontal or X axis. Read the alcohol concentration on the vertical or Y axis.
Using the table find the ratio and the corresponding alcohol concentration.
After calculating the ratio round the number to 4 dismal places. The first two decimals correspond to the numbers on the chart and graph. The third and forth decimals are used to interpolate the concentration between the values given.
The first 3 numbers of the example ratio 1.15 correspond to the number on the chart for 62.20% alcohol concentration. The next higher ratio is 1.16 which corresponds to 65.79% alcohol concentration.
The last two numbers are used to interpolate between the ratios 1.15 and 1.16. Treat the last two numbers as a percentage of the value between 62.2 and 65.79. In the example the last two numbers become 56% (0.56) of the difference between 65.79 and 62.20.
65.79 - 62.20 = 3.59
3.59 x .56 = 2.01
62.2 + 2.01 = 64.21
Add the difference to the lower number which yields the alcohol concentration.
For alcohol soaking purpose it is not necessary to do the math to determine an exact percentage of alcohol concentration. A ballpark number is good enough.
Experience has shown that higher concentrations of alcohol in the soaking solution will produce the best results of faster drying times with less degradation of the piece. Therefore it is recommended that the starting alcohol concentration be greater than 60%.
Wood can be successfully dried with lower concentrations but the advantages of soaking in alcohol are diminished. Drying time will increase. Because there is more water in the wood, which does not migrate out of the wood as easily as alcohol, more stress will develop across the walls of a piece which increases the probability of cracking.
It is only necessary to weigh the water once as long as the same bottle is used for weighing the solution sample. The water weight for the bottle used in the example will always be 609g. For subsequent test it will only be necessary to weigh a solution sample.
After weighing the solution rinse out the bottle with a small amount of alcohol and add it to the solution container. Compressed air blown into the inverted bottle will insure it is dry.
Alcohol Percentage Graph and Table is available in JPG format. Print a copy of the chart for your convenience.
The phenomenon of miscibility is key to drying wood by alcohol soaking. Miscible liquids will reach a uniform concentration when combined in a container. An example is a bottle of wine which maintains a uniform consistency of alcohol and water no matter how long it sets undisturbed.
When a piece of wood is placed in an alcohol solution the phenomenon of miscibility will cause the water in the wood and the alcohol in the solution to migrate until they reach equilibrium. The final alcohol concentration in the wood will always be less than the starting alcohol concentration of the soaking solution.
Replacing water in wood with alcohol is the key mechanism for drying wood faster. Alcohol readily moves through cell walls and has a lower vapor pressure than water. As the concentration of alcohol in the wood goes down the drying time increases. Therefore, it is useful to know the alcohol concentration of the soaking solution.
A hydrometer is one way to measure alcohol concentration. To be more accurate the temperature of the solution needs to be measured to correct for density changes due to temperature. The easiest way to measure temperature is to use a hydrometer with an integrated thermometer. Hydrometers are expensive and breakable. Since a scale is needed to track the drying of wood pieces a method of determining alcohol concentration by weight would utilize existing equipment and minimize cost.
Knowing that alcohol and water have different densities I concluded that the alcohol concentration of a solution could be calculated by a ratio of weights. I contacted Professor Shawn Bearden in Pocatello, ID and ask him if he could help me devise a procedure. Shawn developed the graph and table used in this procedure.
The procedure requires the following:
A scale capable of measuring a minimum of 1 gram(g) increments.
A see through container with a narrow neck to increase the accuracy of the sample size to be weighed.
A copy of the Alcohol Percentage Graph and Table
This water bottle has a color change near the top which is used for the measuring line.
1. Select a narrow neck vessel for weighing the samples. I prefer to use plastic since I am sure I will drop it sooner or later. A salad dressing bottle or water bottle make good sample vessels.
2. Draw a line about an inch below the top of the sample container. The line needs to be narrow enough to accurately measure each sample.
3. Weigh the empty container and record the weight.
4. Fill the container to the line with water.
5. Weigh the sample and record the weigh.
6. Empty the container and fill it with soaking solution to the measuring line.
7. Weigh the sample and record the weight.
Calculating the weight ratio.
The ratio is calculated by dividing weight of the water by weight of the solution. To be more accurate subtract the weight of the empty bottle from water and solution weights.
2. Draw a line about an inch below the top of the sample container. The line needs to be narrow enough to accurately measure each sample.
3. Weigh the empty container and record the weight.
4. Fill the container to the line with water.
5. Weigh the sample and record the weigh.
6. Empty the container and fill it with soaking solution to the measuring line.
7. Weigh the sample and record the weight.
Calculating the weight ratio.
The ratio is calculated by dividing weight of the water by weight of the solution. To be more accurate subtract the weight of the empty bottle from water and solution weights.
(Weight of water) - (weight of bottle) /(Weight of solution) - (weight of bottle)
Empty bottle weight equals 23g.
Water sample weight equals 632g.
Solution sample weight equals 550g.
632g - 23g /550g - 23g 609g /527g = 1.155597
The resulting quotient is the ratio and will be a number greater than 1.
Rounded to 4 dismal places, ratio = 1.1556
Converting the quotient to percentage of alcohol concentration.
Using the graph find the ratio on the horizontal or X axis. Read the alcohol concentration on the vertical or Y axis.
Using the table find the ratio and the corresponding alcohol concentration.
After calculating the ratio round the number to 4 dismal places. The first two decimals correspond to the numbers on the chart and graph. The third and forth decimals are used to interpolate the concentration between the values given.
The first 3 numbers of the example ratio 1.15 correspond to the number on the chart for 62.20% alcohol concentration. The next higher ratio is 1.16 which corresponds to 65.79% alcohol concentration.
The last two numbers are used to interpolate between the ratios 1.15 and 1.16. Treat the last two numbers as a percentage of the value between 62.2 and 65.79. In the example the last two numbers become 56% (0.56) of the difference between 65.79 and 62.20.
65.79 - 62.20 = 3.59
3.59 x .56 = 2.01
62.2 + 2.01 = 64.21
Add the difference to the lower number which yields the alcohol concentration.
For alcohol soaking purpose it is not necessary to do the math to determine an exact percentage of alcohol concentration. A ballpark number is good enough.
Experience has shown that higher concentrations of alcohol in the soaking solution will produce the best results of faster drying times with less degradation of the piece. Therefore it is recommended that the starting alcohol concentration be greater than 60%.
Wood can be successfully dried with lower concentrations but the advantages of soaking in alcohol are diminished. Drying time will increase. Because there is more water in the wood, which does not migrate out of the wood as easily as alcohol, more stress will develop across the walls of a piece which increases the probability of cracking.
It is only necessary to weigh the water once as long as the same bottle is used for weighing the solution sample. The water weight for the bottle used in the example will always be 609g. For subsequent test it will only be necessary to weigh a solution sample.
After weighing the solution rinse out the bottle with a small amount of alcohol and add it to the solution container. Compressed air blown into the inverted bottle will insure it is dry.
Alcohol Percentage Graph and Table is available in JPG format. Print a copy of the chart for your convenience.
Saturday, November 04, 2006
Order your shirts before they are gone.
There are only a few alcohol soaking shirts left. At the present I do not plan to order more shirts unless there are a large number of requests. The shirts are $14.95 plus $4.50 shipping and handling to United States addresses. You can order the shirts here.
As of Saturday evening November 4th the remaining number of shirts:
Time is Fine
6 - Large
2 - Medium
Don't Turn
1 - Extra Large
4 - Large
3 - Medium
Shirt sales have been the main source of financial support to offset the cost of testing and perfecting the alcohol drying protocol. I continue to refine the process and disseminate information as time permits. Thanks to all the people who purchased shirts and supported my efforts.
Several people have suggested I produce a video on the alcohol drying process. At this time I have not been convinced that sales of a video would yield enough return to justify the cost. Please take the time to email me your thoughs on the issue.
As of Saturday evening November 4th the remaining number of shirts:
Time is Fine
6 - Large
2 - Medium
Don't Turn
1 - Extra Large
4 - Large
3 - Medium
Shirt sales have been the main source of financial support to offset the cost of testing and perfecting the alcohol drying protocol. I continue to refine the process and disseminate information as time permits. Thanks to all the people who purchased shirts and supported my efforts.
Several people have suggested I produce a video on the alcohol drying process. At this time I have not been convinced that sales of a video would yield enough return to justify the cost. Please take the time to email me your thoughs on the issue.