Silktree Closed Form
I started turning this piece about 2 weeks ago. I had it roughed out and just started to hollow it when I had to set it aside. Put it into a paper bag packed in wet shavings. The log was cut last November and sat outside with the ends sealed until the end of May. The pith is not sound but I wanted to turn a whole log hollow form to show off the grain.
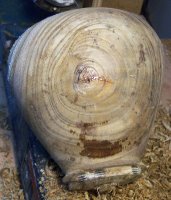
I applied super glue to the cracks around the pith before packing the partially turned piece in shavings.
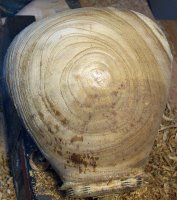
When I put the roughed out piece into the alcohol there was no further cracking. I have successfully dried pieces with the pith in the sides using the alcohol soaking protocol. This is my first attempt with silktree.
I did not check the concentration of alcohol before putting the piece in the bucket. If the ending alcohol percentage is above 70% then I expect the piece to be dry in 5 to 7 days. Silktree is quite porous which allows it to lose moisture quickly.

Diameter: 7.5"
Height: 7.5" including tenon
Wall thickness: 0.5"
Rim opening: 2.5"
Bowl into alcohol solution: 2145, 06/10/2006
Bowl out of soaking solution:
Alcohol percentage of solution:
Begin soak: Did not measure.
End soak: 65.5% *
Weight in grams
06/11 - 1100 - 1286
06/11 - 2145 - 1184
06/12 - 0905 - 1112
06/12 - 2115 - 1070
06/13 - 0815 - 1034
06/13 - 2130 - 1002
06/14 - 0930 - 979
06/14 - 2300 - 956
06/15 - 1330 - 937
06/16 - 1245 - 907
06/17 - 0715 - 883
06/18 - 0915 - 857
06/19 - 1400 - 840
06/20 - 1330 - 828
06/21 - 2015 - 812
06/22 - 1400 - 807
6/23 - 2200 - 795
6/24 - 1400 - 794
6/25 - 1530 - 793
6/26 - 1500 - 791
6/27 - 2000 - 790
6/28 - 1500 - 788
6/29 - 1530 - 790
7/16 - 1000 - 789
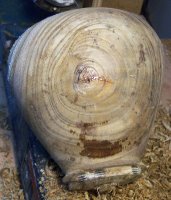
I applied super glue to the cracks around the pith before packing the partially turned piece in shavings.
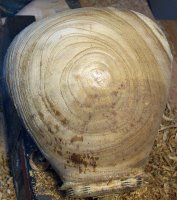
When I put the roughed out piece into the alcohol there was no further cracking. I have successfully dried pieces with the pith in the sides using the alcohol soaking protocol. This is my first attempt with silktree.
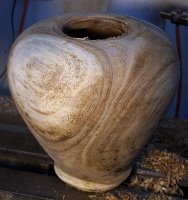

Fresh out of the alcohol.
Silktree from Gresham. OR. Cut down 11 November 2005.Diameter: 7.5"
Height: 7.5" including tenon
Wall thickness: 0.5"
Rim opening: 2.5"
Bowl into alcohol solution: 2145, 06/10/2006
Bowl out of soaking solution:
Alcohol percentage of solution:
Begin soak: Did not measure.
End soak: 65.5% *
Weight in grams
06/11 - 1100 - 1286
06/11 - 2145 - 1184
06/12 - 0905 - 1112
06/12 - 2115 - 1070
06/13 - 0815 - 1034
06/13 - 2130 - 1002
06/14 - 0930 - 979
06/14 - 2300 - 956
06/15 - 1330 - 937
06/16 - 1245 - 907
06/17 - 0715 - 883
06/18 - 0915 - 857
06/19 - 1400 - 840
06/20 - 1330 - 828
06/21 - 2015 - 812
06/22 - 1400 - 807
6/23 - 2200 - 795
6/24 - 1400 - 794
6/25 - 1530 - 793
6/26 - 1500 - 791
6/27 - 2000 - 790
6/28 - 1500 - 788
6/29 - 1530 - 790
7/16 - 1000 - 789
Silktree
Click on picture to enlarge
* - I have had success soaking bowls in solutions as low as 50% but after further research I don't recommend it. I will add dry alcohol to the solution to bring it to a concentration greater than 70%.
Click on picture to enlarge
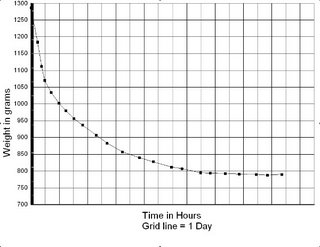
06/24/2006 - Looks as if I missed the drying time on this piece. A combination of low alcohol concentration and the small opening probably lead to the slower drying time. Still, 13 days to dry a closed form is not bad. The piece will probably not lose any significant weight from now on. I will continue to record data for a few more days then unwrap it. There are no indications of degradationon the inside and the pith is intact. Final pictures in a few days.
07/16/2006 - Unwrapped and started to finish the hollow form. Final weight take today is 789 grams. No change in over 2 weeks. Since the 24th of June when I called the piece dry enough for turning it lost a total of 5 grams which represents 1% of the total weight loss.
No degradation of the CA glue I applied to the cracks developing around the pith during rough out.
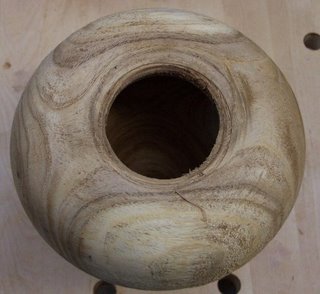
The final measurements at the widest diameter are 7 7/16" by 7 1/4". The piece remounted tightly in the chuck which indicates how little the foot distorted while drying.
Very little material was removed to reture the top opening and the bottom tenon.
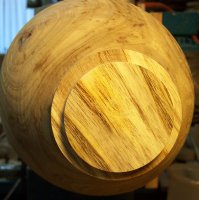
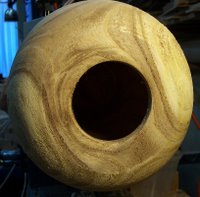
After turning and power sanding to 150 the piece is ready for a coat of finish.
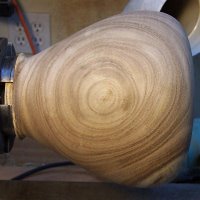
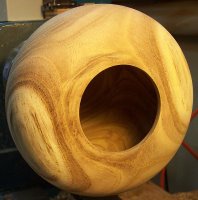
Since silktree is porous and soft. I apply a coat of finish before making any decorative cuts like rings I intend to turn around the opening. The CA glue has been turned away from one pith but is still visible in the other. The crack on the inside is barely visible so I could turn away more material to reduce the crack size visible on the outside.
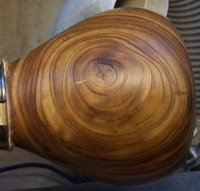
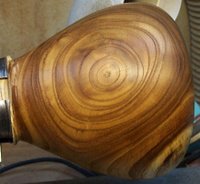
At this point I haven't decided if I want to add a collar.
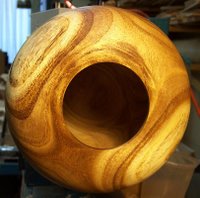
Finish brings out the contrast in the different layers of wood.
The finished piece is available for purchase in the Gift Shop at Wood n Heart.




Finished pictures added 12/22/06.
07/16/2006 - Unwrapped and started to finish the hollow form. Final weight take today is 789 grams. No change in over 2 weeks. Since the 24th of June when I called the piece dry enough for turning it lost a total of 5 grams which represents 1% of the total weight loss.
No degradation of the CA glue I applied to the cracks developing around the pith during rough out.
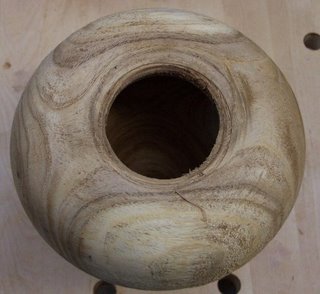
The final measurements at the widest diameter are 7 7/16" by 7 1/4". The piece remounted tightly in the chuck which indicates how little the foot distorted while drying.
Very little material was removed to reture the top opening and the bottom tenon.
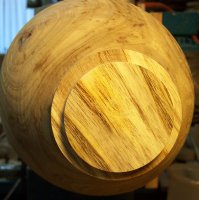
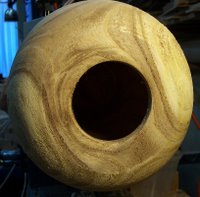
After turning and power sanding to 150 the piece is ready for a coat of finish.
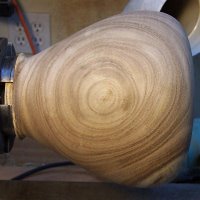
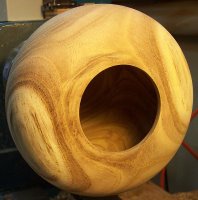
Since silktree is porous and soft. I apply a coat of finish before making any decorative cuts like rings I intend to turn around the opening. The CA glue has been turned away from one pith but is still visible in the other. The crack on the inside is barely visible so I could turn away more material to reduce the crack size visible on the outside.
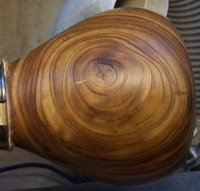
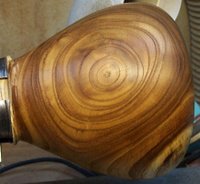
At this point I haven't decided if I want to add a collar.
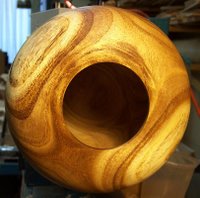
Finish brings out the contrast in the different layers of wood.
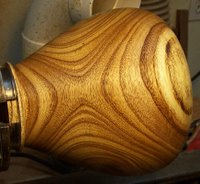
Finished pictures added 12/22/06.